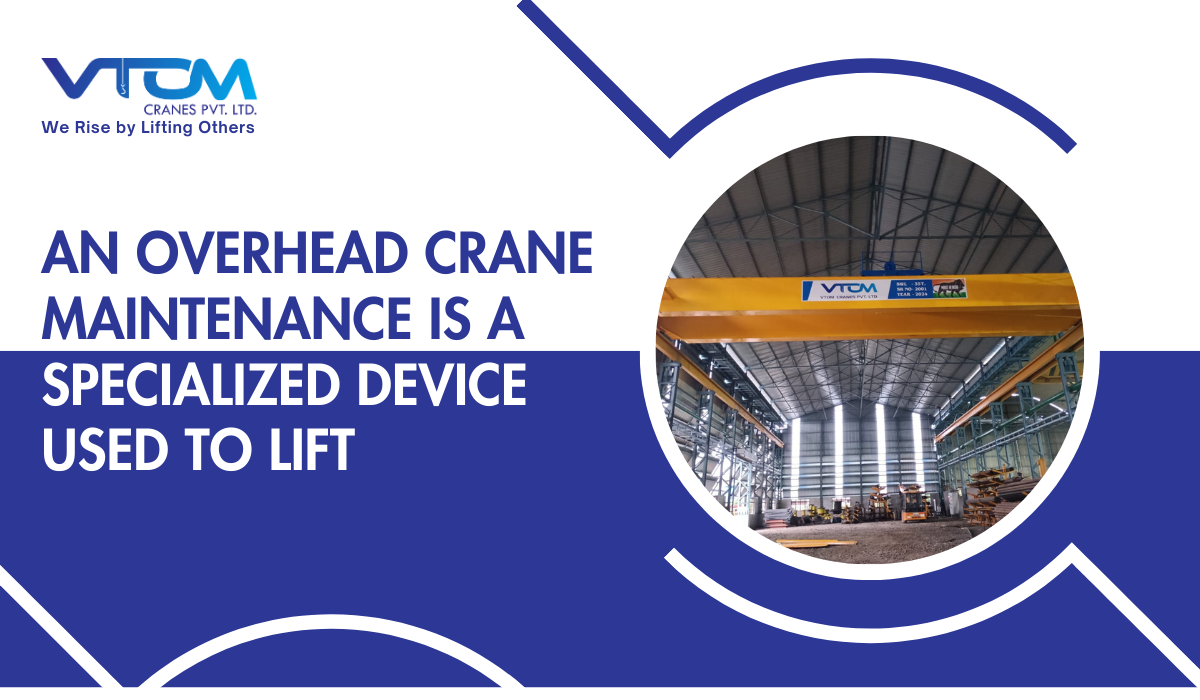
Table of Contents
An overhead crane maintenance is a specialized device used to lift, lower, and move heavy loads horizontally within a defined space. While there are numerous types of cranes, overhead cranes are particularly valuable due to their ability to offer efficient and reliable material handling through their horizontal, rail-mounted support system that spans the workspace. This makes them indispensable in industries such as manufacturing, shipping, and construction.
Like any other industrial equipment, regular maintenance is crucial to ensure optimal performance, maintain safety, and prevent operational disruptions. In this article, we’ll cover common issues encountered during the lifespan of overhead cranes and outline some of the best practices for maintaining them to ensure longevity and safety.
Best Practices for Overhead Crane Maintenance In Pune
Proper maintenance of overhead cranes is essential to not only ensure safety but also to extend the lifespan of this critical equipment. Since overhead cranes are often used in environments where both people and valuable materials are present, maintaining these machines can prevent accidents and equipment damage. Moreover, regular upkeep protects your investment by reducing wear, increasing efficiency, and minimizing downtime due to repairs.
By implementing a solid maintenance plan, operators can significantly reduce the risk of accidents, injuries, and costly operational interruptions. Here are some of the top practices for maintaining overhead cranes –
1. Regular Inspections
Consistent inspections are one of the most effective ways to identify potential issues before they escalate into more serious problems. It’s recommended to have daily, monthly, and yearly inspection schedules.
- Daily Inspections: Before each shift, a basic check should be conducted to look for visible signs of wear, loose or damaged parts, and any strange noises during operation. Additionally, ensure that emergency stop buttons and safety switches are functioning properly.
- Monthly Inspections: These are more thorough and involve checking electrical connections, inspecting wire ropes or chains for wear, and examining structural components for cracks or deformities. Using an inspection checklist and following the manufacturer’s maintenance schedule can be particularly helpful.
- Annual Inspections: An in-depth examination should be conducted at least once a year by a certified inspector. This comprehensive inspection should cover all major crane components, including load-bearing elements, hoists, brakes, and control systems to ensure everything is in working order.
2. Follow the Manufacturer’s Guidelines
When an overhead crane is installed, it represents a significant financial investment. To protect this investment, the manufacturer provides a detailed maintenance manual or schedule that outlines the necessary service steps, such as lubrication schedules and inspection intervals based on the crane’s duty cycle.
Strictly adhering to these guidelines ensures that your crane is running efficiently and prevents premature wear or unexpected breakdowns. Following the manufacturer’s instructions for maintenance also ensures the crane’s warranty remains valid.
3. Lubrication and Cleaning
Lubrication is critical to reducing friction and wear on the crane’s moving parts. Key components such as wire ropes, sheaves, gears, and bearings should be regularly lubricated to prevent damage from excessive friction. Routine cleaning is equally important, as it helps remove corrosive substances, dirt, and debris that can negatively affect the crane’s performance over time.
4. Consider the Operating Environment
The environment in which the crane operates plays a significant role in its longevity and maintenance needs. Factors such as extreme temperatures, high humidity, dust, chemical exposure, and steam can accelerate wear on the crane’s components. Protective coatings on metal parts can help mitigate some of these environmental risks.
Proactively considering the crane’s working environment during its installation and design can prevent long-term damage, such as corrosion or dirt accumulation, which can otherwise shorten its lifespan.
5. Operator Training and Education
Effective maintenance is not only the responsibility of maintenance staff but also of the crane operators. Proper training ensures that operators are familiar with safe operational techniques, the crane’s specific requirements, and how to spot early signs of wear or malfunction.
Training programs should cover topics such as lubrication practices, inspection protocols, and the importance of reporting any abnormalities immediately. Well-trained operators help ensure the crane operates efficiently and safely, reducing the need for repairs.
Common Issues with Overhead Cranes
Even with routine maintenance, overhead cranes may experience certain issues over time. Being aware of these problems can help operators and engineers address them promptly, ensuring minimal downtime and repair costs.
1. Electrical Problems
Electrical issues are common in overhead cranes and can be caused by faulty wiring, loose connections, or malfunctioning motors. These issues may result in erratic crane movement, power outages, or electrical hazards.
Some frequent electrical problems include –
- Contact Interruptions – Poor contact between the conductor bars and collectors can lead to operational disruptions. This is often caused by the buildup of carbon graphite dust or corrosion on the copper rails.
- Push Button and Radio Control Failures – Environmental factors, such as radio interference from nearby industrial processes like induction welding, can disrupt communication between radio controls and the crane. Over time, push buttons or radio controls may become less responsive, requiring repairs or replacements.
- Circuit Faults – If the crane blows fuses frequently, it may be a sign of a faulty circuit. A qualified crane service provider should be contacted to diagnose and fix the issue promptly.
2. Wear and Tear
Over time, various parts of the crane, such as wire ropes, pulleys, and gears, will wear out. If not addressed promptly, this can lead to reduced lifting capacity and even dangerous situations. Components like end truck wheels often require adjustment or replacement due to natural wear, and improper rail alignments can exacerbate this wear.
Having the crane’s runway system properly designed, inspected, and maintained by a reliable manufacturer is crucial to preventing premature wear and misalignment.
3. Misalignment
Crane misalignment occurs when the structure or its components are not correctly aligned. This can result in uneven load distribution, causing strain on specific parts of the crane and increasing the risk of failure. A crane that’s misaligned on its runway may experience significant stress, leading to structural damage or failure. Regular inspections and adjustments are necessary to correct any misalignment issues early on.
4. Deformed or Faulty Hooks
Crane hooks play an integral role in supporting loads, and any deformation can compromise their integrity. Bent, stretched, or cracked hooks increase the risk of load slippage, which can cause accidents. Regular inspections of the hook and other rigging hardware are essential to ensure their reliability and safety.
Conclusion
Regular maintenance of overhead cranes is critical for optimizing performance, reducing repair costs, and ensuring the safety of workers and assets. By conducting routine inspections, adhering to the manufacturer’s guidelines, and addressing common issues like electrical problems, wear and tear, misalignment, and faulty hooks, you can extend the lifespan of your crane and avoid costly downtime.
Tag – Overhead Crane Maintenance In Chikhali, Overhead Crane Repair In Chikhali, overhead crane maintenance In Bhosari Pune, Overhead Crane Repair In Bhosari Pune, Overhead Crane Maintenance In PCMC, Overhead Crane Repair In PCMC, overhead crane maintenance In PCMC Pune, Overhead Crane Repair In PCMC Pune